With more than 40 years of large-scale industrial adsorption and ion exchange experience, ARi provides scalable technology and equipment for the direct lithium extraction industry.
ARi has been providing customers with adsorption and ion exchange technology on a large industrial scale for more than 40 years. With our deep knowledge of the operations involved, we fully understand the critical challenges for commercialising direct lithium extraction (DLE) technology on an industrial scale.
Important issues that need to be considered during commercialisation include:
- The adsorbent (including its capacity, cost, longevity and the impact of these factors on the operating cost of the plant);
- The process technology to be used;
- The equipment to be installed (including the reliable scale-up of this equipment to large industrial sizes); and
- The impact of the performance of the DLE operation on the performance and economics of the downstream processing steps.
Due to the relatively low lithium concentration in the brines to be processed, most DLE operations must be carried out at very high brine throughputs. Construction of the largest possible adsorption vessels will, therefore, be critical to minimising the capital cost of the process.
ARi’s unique experience in the direct lithium extraction industry
ARi is in a relatively unique position in the DLE industry – having an extensive track record of providing adsorption and ion exchange equipment on the industrial scale appropriate for direct lithium extraction operations while also offering proprietary fractal fluid distribution technology that allows for the simple and reliable scale-up of adsorption operations from pilot-scale testing to full commercial-scale operation at very low risk.
Since the 1980s, ARi has been providing adsorption, ion exchange and chromatography systems to industrial customers on a very large scale. Typical examples would include the production of high fructose corn syrup production for beverage use or beet molasses desugarisation in the sugar industry, where ARi is undoubtedly the world’s leading technology and equipment supplier.
In collaboration with their engineering licensee in these markets, Escon GmbH, ARi has provided more than 25 systems in the beet sugar industry alone, employing resin columns with diameters greater than 6.7m (or 22 ft) and total installed resin volumes of the order of 1,000m3 (35,000 ft3) or greater.
This scale is of the same order of magnitude as is expected to be typical for DLE. Outside of the sugar and sweetener industries, commercial ion exchange, adsorption or chromatography installations of this size are relatively rare, with very few other technology and equipment suppliers having any track record of successful installations.
Tailored solutions
As well as being an industry-leading provider of technology and equipment in a range of markets, including DLE and lithium polishing, ARi works with customers to develop innovative processes to meet their specific separation challenges. This service can include the characterisation and selection of resins or adsorbents at a laboratory scale, optimisation and performance testing of the separation process at the pilot scale, and scale-up to a commercial-scale installation.
Based on expertise gained through decades of experience with resin-based and adsorbent-based separations, ARi can provide customers with a comprehensive overview of their target separation, its sensitivity to changes in operating parameters and its impact on downstream processing operations. This lets customers comprehensively optimise their process economics and performance.
In addition, ARi’s unique fractal fluid distribution technology allows industrial separation processes to be scaled up to very large vessel sizes with complete confidence, reducing the risk to the customer during commercialisation.
The risks of scale-up
The typical path of a technology development project passes through stages of laboratory-scale testing, pilot-scale testing (perhaps at more than one scale), demonstration-scale testing and then full-scale commercial implementation.
The reason for carrying out testing at ever-increasing scales is to understand how changes in equipment size affect the physical and chemical phenomena involved in the various unit operations of the overall process. It is well known that many processes do not scale predictably. This typically leads to a reduction in process performance as the size of the equipment involved increases, caused by increasing inefficiencies in the physical and chemical operations involved (particularly operations such as fluid distribution and mixing).
To counteract this effect, some oversizing of equipment is usually required, increasing the project’s capital cost. The relatively unknown impact of equipment size on performance makes scale-up an inherently risky undertaking, as the possibility exists that the full-scale commercial implementation of the process may not work as expected.
Traditional versus ARi fluid distributors
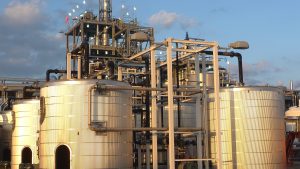
High-quality plug flow fluid distribution is critical to the performance of adsorption and ion exchange operations, particularly in the larger equipment sizes used for commercial separations. By minimising unwanted fluid mixing and sharpening the breakthrough interface between different fluids in a bed of resin or adsorbent, a high-quality fluid distribution will:
- Maximise the effective use of the resin or adsorbent, thereby reducing capital costs;
- Minimise the use of chemical regenerants or eluents, thereby reducing operating costs; and
- Minimise product dilution and wastewater generation.
The fluid distributors used in conventional ion exchange or adsorption applications (such as radials, laterals or nozzles) do not distribute flow effectively over the entire cross-section of the column area, especially at larger scales. Consequently, fluid flows preferentially through certain portions of the resin bed (known as ‘channelling’) while other portions remain under-utilised.
This is evident when carrying out a tracer test using blue dye to assess the quality of fluid distribution achieved. The concentration front within the adsorbent bed spreads due to the inefficient distribution, leading to a more diffuse breakthrough curve with early leakage, reducing the efficiency of the adsorption process. This effect becomes greater as the diameter of the adsorbent vessel increases, leading to more significant reductions in performance when compared to the pilot scale and increasing the unpredictability of scale-up.
By contrast, ARi uses proprietary fractal fluid distribution technology designed to distribute fluid flow geometrically, utilising a network of fluid channels with a high degree of symmetry. The hydraulic path that each portion of the fluid travels from the central inlet to each outlet is exactly the same, including the same number of 90° bends. This allows for a precise and uniform fluid distribution unaffected by factors such as the flow rate or the pressure drop of the flow path.
Traditional fluid distributor types used in the chemical process industries make use of a controlled pressure drop across orifices, nozzles or screens to produce a distribution of the process fluid. However, the pressure drop through these orifices, nozzles, or screens changes substantially as the flow rate varies. As a result, a fluid distributor that may work adequately at one design flow rate will perform very poorly at any other flow rate, resulting in a very non-uniform fluid distribution.
This is a severe disadvantage for industrial processes that depend on a plug flow distribution of the process fluid for their efficiency and performance. This problem is so severe in ion exchange applications that equipment suppliers often install two sets of fluid distributors within the same vessel – one for high rates of flow and another for operation at lower rates of flow.
De-risking scale-up
Fractal fluid distributors do not depend on a controlled pressure drop for efficient operation. Instead, they use their highly symmetrical structure to create a dense, uniform distribution of fluid across a surface area, which remains the same regardless of the pressure drop across the distributor. Typically, ARi fractal distributors operate with a negligible pressure drop (usually below 15 kPa or two psi) and are capable of very large turndown ratios in the flow rate of ten to one or more without any reduction in plug flow performance.
As a result of the highly symmetrical nature of its design, fractal fluid distribution can easily be scaled to any size. Since every hydraulic flow path within a fractal fluid distributor is identical, each flow path behaves in the same way, regardless of the size of the fluid distributor or the number of flow paths. This allows fluid distributors to be scaled up to very large sizes with complete reliability and predictability.
Consequently, industrial processes, such as ion exchange, adsorption and industrial chromatography, can be tested at a relatively small scale and then scaled up to a full commercial-scale implementation without risk of reduced performance. This is impossible with the other fluid distributor types used in these applications,
which increasingly lose effectiveness at larger sizes and result in full-scale industrial performance that is inferior to that achieved on a pilot scale. The use of fractal fluid distribution thus significantly de-risks the scale-up of industrial technologies that are implemented on a very large scale, such as direct lithium extraction.
It also saves money and time in the technology development process by potentially eliminating one or more scale-up steps (such as the relatively expensive demonstration-scale stage). For example, ARi routinely scales up industrial processes from pilot scale tests carried out in resin or adsorbent columns of 80mm (three inches) in diameter to full-scale commercial installations with vessel diameters greater than six metres (20ft) while successfully providing process performance guarantees on the resulting systems.
ARi has already provided fractal fluid distribution technology to the lithium industry on an industrial scale, with the first DLE facility using this technology planned to go into commercial production in mid-2024.
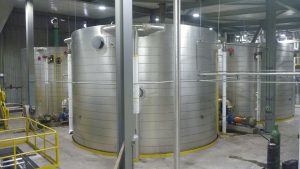
In addition to providing industrially-proven equipment and fluid distribution technology to de-risk scale-up, ARi has also developed proprietary direct lithium extraction process technology that can be tailored to various brine compositions and ion exchange technology for the polishing of lithium-rich brines to remove divalent cations and boron.
Contact ARi to learn more about how we can help bring your lithium project to low-risk commercial-scale operation using technology and equipment solutions proven over more than 40 years at a large industrial scale.
Please note, this article will also appear in the seventeenth edition of our quarterly publication.