Ford’s EV & Battery Manufacturing Ambitions Get A Boost With Rockwell Automation Technologies
Last year, CleanTechnica reported on the collaboration between Ford Motor Corp. and Rockwell Automation for automation on the shop floors of the Ford Blue Oval City, an approximately $6 billion mega manufacturing facility in Stanton, Tennessee. Once fully operational, the factory can create approximately 6,000 new jobs and, according to Ford, will “reimagine how vehicles and batteries are manufactured.”
Ford is building a second plant in Glendale, Kentucky, for batteries alone. The company officially broke ground for the plant on December 5 of last year. Called the Ford Blue Oval SK Battery Park, the $5.8 billion project will produce batteries for the Ford and Lincoln EV lines and in turn create 5,000 new jobs in the town.
While the commencement of production at Blue Oval SK 2 faced delays, construction is steadily progressing. These setbacks were officially acknowledged by the company in October 2022, with reasons attributed to various factors such as the global chip shortage and mounting inflation. Ford has not disclosed a revised starting date for production at the battery plant.
Since construction of the plant continues to proceed according to the original schedule, Ford’s technical partners like ABB and Siemens also continue their plans for outfitting the plant with their automation and digitalization solutions for the new factories. Siemens has its Manufacturing Operations Management (MOM) software, which will help Ford to optimize its production processes, while ABB is providing its robots and other automated manufacturing solutions for the new plants.
Closer to home is Rockwell Automation. The American automation technology provider will supply Ford the various process automation systems which will help Ford to control and monitor its production equipment.
Rockwell Automation indicates it is at the forefront of innovation in the electric vehicle (EV) manufacturing, motor, and battery industries. The company operates an 8,000 square-foot Electric Vehicle Innovation Center in San Jose, California, where automotive startups and established manufacturers go to participate in an interactive learning environment which, since 2019, showcases an evolution of the latest EV manufacturing technologies, including AR/VR modeling, state-of-the-art battery pack assembly machines, cutting-edge robot technologies, and rigorous functional testing.
These innovations are helping manufacturers like Ford, Tesla, and Rivian to produce EVs more efficiently, reliably, and sustainably. Here is a detailed look at some of Rockwell Automation’s key innovations in these areas:
Integrated Architecture System
The Integrated Architecture system is Rockwell Automation’s next-generation automation system. It is designed to help manufacturers achieve their digital transformation goals by connecting and controlling all aspects of their operations, from the edge to the cloud.
The Integrated Architecture system is used by automakers to connect and control all aspects of their EV production operations, from the battery cell manufacturing process to the final assembly line. This connectivity allows automakers to optimize their EV production operations and improve the efficiency and quality of their EV products.
FactoryTalk InnovationSuite
FactoryTalk InnovationSuite is a suite of software tools that can be used to collect, analyze, and visualize data from EV production operations. FactoryTalk InnovationSuite can help automakers to identify areas for improvement in their EV production operations and to make better decisions about their operations.
For example, automakers can use FactoryTalk InnovationSuite to identify trends in their EV production data and to identify potential problems before they occur. This can help automakers to improve the uptime of their EV production lines and to reduce the number of defective EVs produced.
Connected Enterprise Platform
The Connected Enterprise platform is Rockwell Automation’s cloud-based platform that allows manufacturers to connect their EV production operations to the cloud. This connectivity allows automakers to share data between different parts of the EV production process and to collaborate with suppliers and partners.
For example, automakers can use the Connected Enterprise platform to share data about their EV production plans with their suppliers. This can help suppliers to better plan their own production operations and ensure that they have the necessary components on hand to meet the demands of the automakers.
Electric Vehicle Battery Testing & Simulation Solutions
Rockwell Automation offers a variety of testing and simulation solutions for EV batteries. These solutions can be used to test the performance and reliability of EV batteries under different conditions, such as extreme temperatures and high-power charging.
Automakers use Rockwell Automation’s electric vehicle battery testing and simulation solutions to ensure that their EV batteries meet their high standards for performance and reliability. This helps automakers to produce safe and reliable EVs for their customers.
Electric Vehicle Motor Control Solutions
Rockwell Automation offers a variety of motor control solutions for EVs. These solutions can be used to control the performance of EV motors and to improve the efficiency and reliability of EV powertrains.
Automakers use Rockwell Automation’s electric vehicle motor control solutions to produce EVs with high performance, long range, and fast charging times. This helps automakers to meet the demands of their customers and to produce EVs that are competitive with gasoline-powered vehicles.
Rockwell Automation’s innovations in the automotive EV manufacturing, motor, and battery industries are helping automakers to produce EVs more efficiently, reliably, and sustainably. These innovations are also helping to accelerate the adoption of EVs and to make EVs more affordable and accessible to consumers.
Note: This article was written from available press releases and process/product information from Rockwell Automation. Its purpose is to start off a series of articles on automation and sustainable manufacturing in the electric vehicle manufacturing sector.
Have a tip for CleanTechnica? Want to advertise? Want to suggest a guest for our CleanTech Talk podcast? Contact us here.
Latest CleanTechnica.TV Video
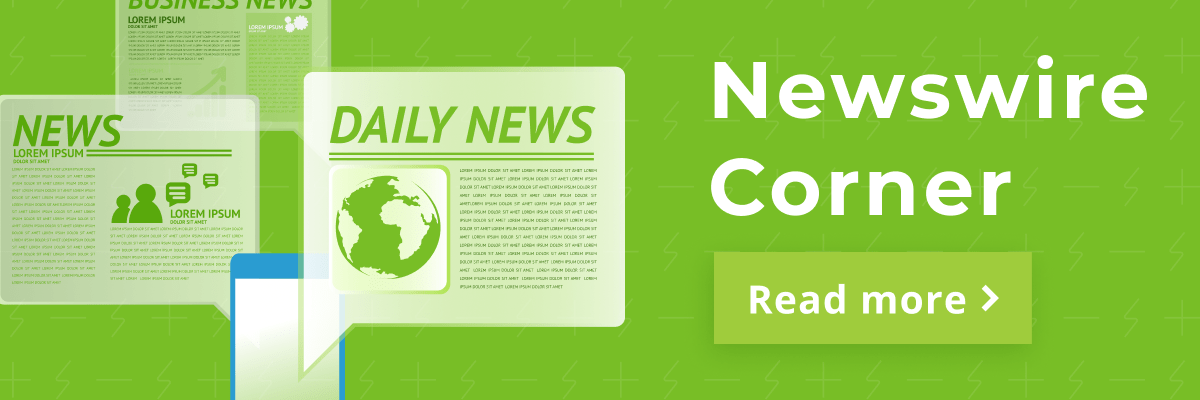
CleanTechnica uses affiliate links. See our policy here.