Moog & Komatsu To Demonstrate Fully Electric Wheel Loader Later This Month
In a recent announcement, Moog Construction and Komatsu said they’re planning to show off their latest loader design. Not only is it battery-powered, but it’s all electric (not hydraulic) and has smart controls that can let manufacturers do a lot more with construction equipment in the future.
Komatsu and the other companies will show off the machine that is battery-powered, zero-emission, and ready for automation at bauma 2022 from October 24 – 30. But, it seems pretty clear that they are trying to get people to go look, so let’s take a look at what they’re going to put on display and demonstrate!
A traction motor, lift, tilt, and steering electric cylinders, power electronics, system control computer, battery, and battery management system are among the components of Moog’s intelligent machine electrification system. The all-electric actuators and motors provide the muscle while the integrated software serves as the system’s brain to connect and intelligently coordinate actions across the machine. Industry leading system efficiency and controllability is possible thanks to the integrated nature of the system.
Komatsu oversaw the vehicle design and manufacturing, including structural configurations that take advantage of Moog’s intelligent machine electrical engineering.
“To achieve our CO2 emission reduction targets from products in use 50% by 2030 from 2010 levels, to achieve carbon neutrality by the end of 2050, we are looking for promising technologies from suppliers to accelerate our electric machine development,” said Seiichi Fuchita, Chief Technology Officer (CTO) and President of Development Division Komatsu. “The machine, built together with Moog, combines the strengths of both companies, and was finalized within a short period of time. We expect the joint testing will show the advantages of a fully electric machine and will prove collaboration is beneficial for both sides.”
The Moog system enables customers to develop their own unique solutions and bring their vision for next-generation machines to life, while lowering development expenses and the time it takes to bring products to market by seamlessly integrating multiple subsystems such as power management, motion control, connectivity, and automation.
After bauma 2022, Moog and Komatsu will test their all-electric loader jointly to affirm the validity of the concept. They believe that this new level of loader efficiency will be achieved, as well as a novel degree of comfort for those who operate it. The companies’ joint test will thus depict an extended machine operating cycle with several assist functions implemented to provide a fatigue-proof and comfortable environment for managing not only the machines but also their day-to-day tasks.
Moog has a long history of converting hydraulic systems to electric in sectors such as aerospace, defense, and industrial machinery for uses including simulators for air, sea, and land vehicles. The Komatsu intelligent machine electrification system will assist Komatsu in managing not just the loader’s motion but also its energy consumption to improve run-time and save money when compared to diesel alternatives.
“Our focus is accelerating electrification, automation, and connectivity by enabling the world’s safest, most sustainable, and most productive machines,” said Joe Alfieri, vice president and general manager for Moog’s construction business unit. “Our cooperation with Komatsu shows that industry leaders in the construction industry are ready for zero-emission machines and we are thrilled to collaborate with them to enable their journey with our production-ready electric, connected and automation systems.”
Moog’s intelligent machine electricity system is meant to be linked, automatable, and scalable to production. The system includes sensing and control capabilities necessary for automation while the integrated software architecture offers built-in tools for managing many axes of motion as well as torque, speed, position, and force with precision. This, combined with the system’s connectivity, will allow Moog’s customers to create and deploy valuable automation capabilities through over-the-air (OTA) feature updates.
Why This Matters
Like a car, converting a piece of construction equipment to run on electric is relatively simple. A combustion engine already makes rotational force, and so can electric motors. So, you replace anything that’s burning dinosaurs to spin and replace it with something that uses a battery’s power to spin. Replace the main engine, of course, but also replace other things like compressors, hydraulic pumps, etc. as well.
But, this just makes the equipment electric, and doesn’t really give the full possible benefits of modern technology. Replacing hydraulic systems with electric systems makes for more efficiency and simpler build/maintenance, and then having a computer directly control those systems gives a lot more flexibility in design and operation.
A great way to illustrate why this is important is to point at Tesla’s upgrade of third brake lights in 2019. To add flashing under certain conditions, most cars would require a hardware upgrade to support the flashing. But, Tesla vehicles were able to make changes like that in the software. This meant that instead of adding hardware, they pushed out an over-the-air update that changed the vehicle’s behavior.
In the case of Moog’s approach to electrifying construction equipment, they aren’t just changing where the energy comes from as much as putting computers in charge of a lot more of the equipment. This means that future construction equipment will be able to get new functionality in some cases with software updates instead of expensive hardware changes. It also means that the toolkit can be used on new equipment designs without having to redesign a bunch of hardware to fit the new machine.
This will not only help the industry move faster and serve people better, but be more efficient overall.
Another important thing is that this approach will allow a lot more remote control of equipment. Sometimes, it can be tough for a machine operator to see the fine details on the ground and see around large parts of the machinery. By being able to get off and make small movements and adjustments while spotting the loader, things will be a lot easier.
More importantly, this level of control also allows for future autonomy. Instead of having one person operate one machine, one might be able to direct the coordinate actions of several machines on a jobsite, telling them overall what to do instead of having to micromanage every little thing like an operator does now.
In other words, it’s a lot easier to say “Go level that area” than it is to run the controls and go do it manually. Automation is going to take the cost savings of software-defined construction equipment to the next level.
All images provided by Moog.
Have a tip for CleanTechnica? Want to advertise? Want to suggest a guest for our CleanTech Talk podcast? Contact us here.
Latest CleanTechnica.TV Video
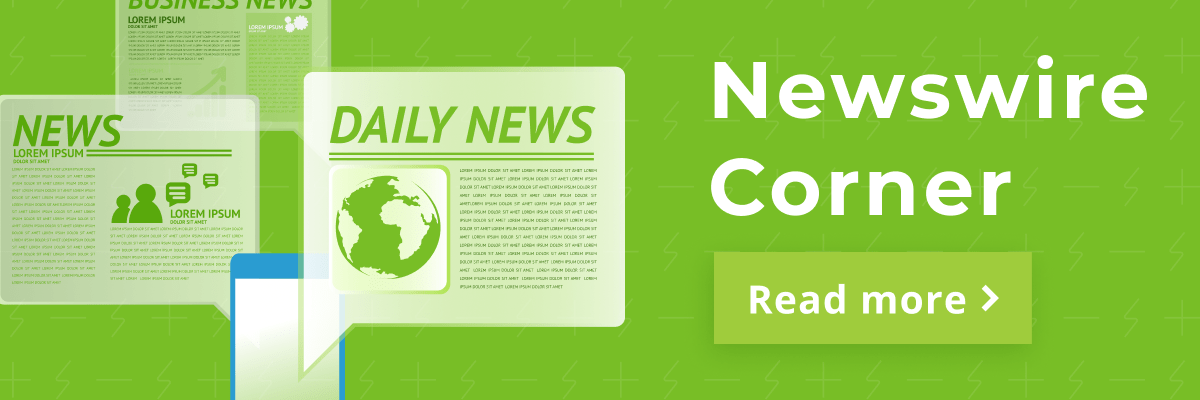
CleanTechnica uses affiliate links. See our policy here.