BASF Will Build A New Battery Recycling Prototype Plant In Southern Brandenburg
BASF has announced plans for a new battery recycling prototype plant in Schwarzheide, which is in the southern part of Brandenburg, Germany, near the Schwarze Elster river. The new plant will be located at the site of its cathode active materials (CAM) plant.
BASF stated that the new prototype plant will recycle end-of-life lithium-ion batteries. The plant will collect lithium, nickel, cobalt, and manganese and will also collect these metals from cell producers and battery material producers.
BASF stated that recycling provides competitive and sustainable access to the necessary metals for CAMs as the demand for EVs continues to increase. The extracted metals will be used to create new CAMs, establishing a circular economy for the battery value chain.
BASF said that its new plant will create around 35 new production jobs and startup is planned for early 2023. The company emphasized the importance of battery recycling as a long-term market requirement in the EV market to reduce the carbon footprint. Another benefit is the plant would help meet the stricter policy measures that are expected under the proposed EU Battery Regulation. That includes recycling efficiencies and material recovery targets for nickel, cobalt, and lithium.
BASF noted that its investment in Schwarzheide reinforces its support of the European Commission’s plans to create a European battery production value chain. The new plant is also part of the Important Project of Common European Interest (IPCEI) that was approved by the European Commission in 2019.
The launch of BASF’s new plant, research to develop battery materials and process development, is funded by the Federal Ministry of Economics. Dr. Matthias Dohrn, Senior Vice President of Precious and Base Metal Services at BASF, said, “With this investment in battery recycling, plus leading process technology for manufacturing of cathode active materials, we aim to ‘close the loop’ while reducing the CO2 footprint of our cathode active materials by up to 60 percent in total compared to industry standards.”
“This will enable us to meet the needs of our automotive OEM customers and helps ensure a more sustainable future for us all.”
Have a tip for CleanTechnica? Want to advertise? Want to suggest a guest for our CleanTech Talk podcast? Contact us here.
Latest CleanTechnica.TV Video
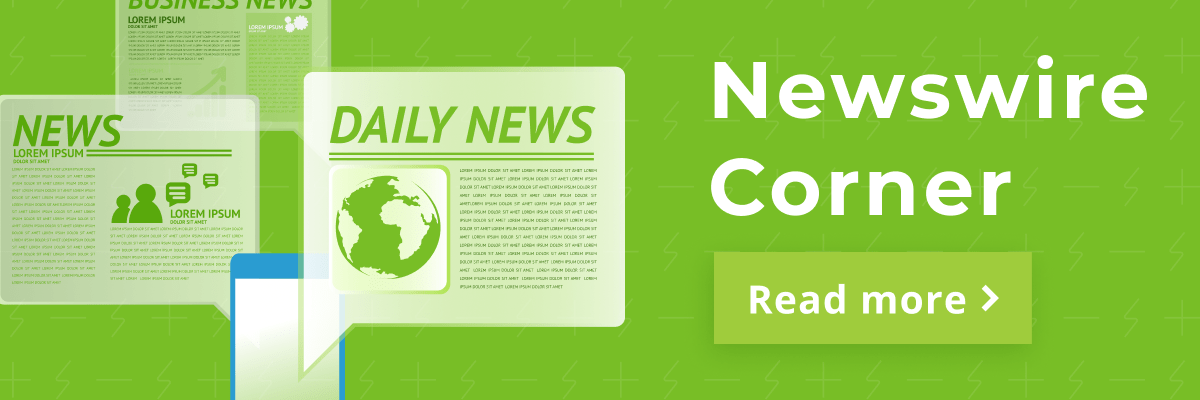
CleanTechnica uses affiliate links. See our policy here.