With Assist From Sustainable Plastics, EV Sets New Speed Record
The Intertubes are buzzing with news that the Formula E electric racing circuit made the Guinness Book of World Records for fastest car indoors when its next-generation GENBETA showcase car hit 218.7 kilometers per hour. The car sports sustainable plastics from the leading Saudi Arabian petrochemical firm SABIC, and that has some interesting implications for sustainable electric cars of the future.
Sustainable Plastics Make Sustainable Cars, But Not Yet
A recent report from the American Chemistry Society sums up the importance of transitioning plastic car parts into a more sustainable supply chain.
According to the ACS report, the typical car contained 411 pounds of plastics in 2021, an increase of 16% since 2012.
“Calculations show those 411 pounds make up less than 10% of an average vehicle’s weight yet approximately 50% of its volume, significantly improving fuel efficiency, and in turn reducing costs for drivers and carbon emissions from transportation,” ACS explained.
“As electric vehicles (EVs) become more popular, plastics are more important than ever to the auto industry. Batteries in EVs are much heavier than internal combustion engines, driving automakers to incorporate more plastic into more components of vehicles, like the chassis and battery casings to offset that additional battery weight,” ACS added.
ACS also noted that certain kinds of high-performance plastics absorb far more crush energy than steel, helping to preserve life and limb in case of a collision.
Sustainable Plastics From A Petrochemical Giant
Under a fossil energy scenario, all this focus on plastic auto parts would be good news for oil and gas stakeholders. However, some petrochemical stakeholders are beginning to respond to the rising demand for more sustainable plastics, and that includes SABIC.
SABIC is not shy about tooting the sustainable horn in the race for fastest indoor electric vehicle. The company has used the GENBETA electric car platform to focus attention on its growing portfolio of sustainable plastic products.
SABIC deployed recycled thermoplastics for GENBETA’s injection-molded wheel fins, which are designed to optimize airflow and reduce drag. “As an additional benefit, the fins can increase the car’s overall efficiency and aid in cooling the brakes to improve stopping power,” SABIC notes.
SABIC also used something it describes as a “bio-renewable, low-carbon material” to fabricate a coated thermoplastic wind deflector. The deflector is another drag reducer.
Rounding out SABIC’s contributions to the fastest indoor speed record are the front wing endplates, formed by a type of 3-D printing process called fused deposition modeling. “They are integral to redirection of airflow around the front wheels to help reduce drag while contributing to the car’s downforce and stability,” SABIC explains.
Apparently, the plastic used in fusion deposition modeling is not part of SABIC’s sustainable plastics portfolio, though the company could eventually take it in that direction.
Recycling Thermoplastics vs. Thermoset Plastics
If you caught that thing about thermoplastics in the GENBETA electric car, that’s of note from a recycling perspective.
Thermoplastics are typically used for lightweight, single-use plastic bottles, films, bags, and food wrappers. They are relatively easy to recycle, because they can be melted and re-formed into new shapes without losing their properties.
Showcasing recycled thermoplastics on the fastest (well, fastest indoor) car in the world can help support the auto’s industry interest in sustainable plastics. However, much of the plastic used in the auto industry is in the category of thermoset plastics, which are different.
Thermoset plastics are favored for durability and heat resistance, but they are much more difficult to recycle than thermoplastics. Instead of melting into a docile puddle when heated, they tend to catch fire.
However, help may be on the way. Back in 2020, MIT News reported on a new method for producing thermoset plastics that could help improve the prospects for recycling. The idea is to add a chemical “linker” that enables thermoset plastics to break down into a powder, which can be re-used to make new plastics without losing their strength.
Researchers at Case Western University have also looked into the matter. They came up with a solvent-assisted process to produce a new class of materials called vitrimer polymers. As of 2020, they were also looking into another process, called mechanochemical ball-milling, that renders thermoset plastics into a powder resin.
Chip in a few dollars a month to help support independent cleantech coverage that helps to accelerate the cleantech revolution!
More Sustainable Plastics From A Petrochemical Giant
SABIC currently produces some of its sustainable plastics with mechanical processes, which involve washing, shredding, and grinding, among other activities. However, the company has made it known that its long-term plans focus on feedstock recycling. That involves pyrolysis, the application of high heat in an oxygen-free environment. Pyrolysis breaks plastic down at the molecular level to form reusable pyrolysis oil.
Pyrolysis has the potential to ramp up the recycling of mixed, post-consumer plastic waste, which is a challenge both on account of the variety of plastics in the mix and the different types of contaminants present in used items.
More Sustainable Plastics For The Electric Vehicle Of The Future
It’s easy to debunk the myth that electric vehicles are somehow less sustainable than gasmobiles (projection, much?), but there is always room for improvement. Plastic plays a key role in the auto parts supply chain, and manufacturers have been on the prowl for recycled and bio-based plastics to play a bigger role.
Ford, in particular, has been front and center in the alternative materials movement. Two recent examples are a partnership with Jose Cuervo on biobased plastics from agave fibers, and a recycled ocean plastic venture. An exploration of dandelion rubber could also pay off, eventually, especially with an assist from the US Department of Defense.
SABIC also took a step in that direction back in 2021, when it introduced its new “ULTEM” resins made from tall oil, a waste byproduct of the wood pulping industry, among other oils.
They may be on to something. Tall oil seems to be catching on in the sustainable plastics field. In May, the Finnish beauty brand Lumene introduced a bio-based plastic jar made from a tall oil material produced by the firm UPM Biofuels, with an assist from SABIC.
TotalEnergies also recently partnered with the French chemical firm Lanxess to produce bio-styrene from tall oil, for use in the wastewater treatment industry.
Note: CleanTechnica has been following the Formula E all-electric racing circuit since its launch in 2015. See our complete coverage here.
Find me on Threads @tinamcasey. Also Post @tinamcasey, or @TinaMCasey on LinkedIn and Spoutible, or @Casey on Mastadon.
Photo: The GENBETA electric race car set a new Guinness record for title fastest speed achieved by a vehicle indoors, with an assist from sustainable plastics from SABIC (photo courtesy of SABIC).
Have a tip for CleanTechnica? Want to advertise? Want to suggest a guest for our CleanTech Talk podcast? Contact us here.
Latest CleanTechnica.TV Video
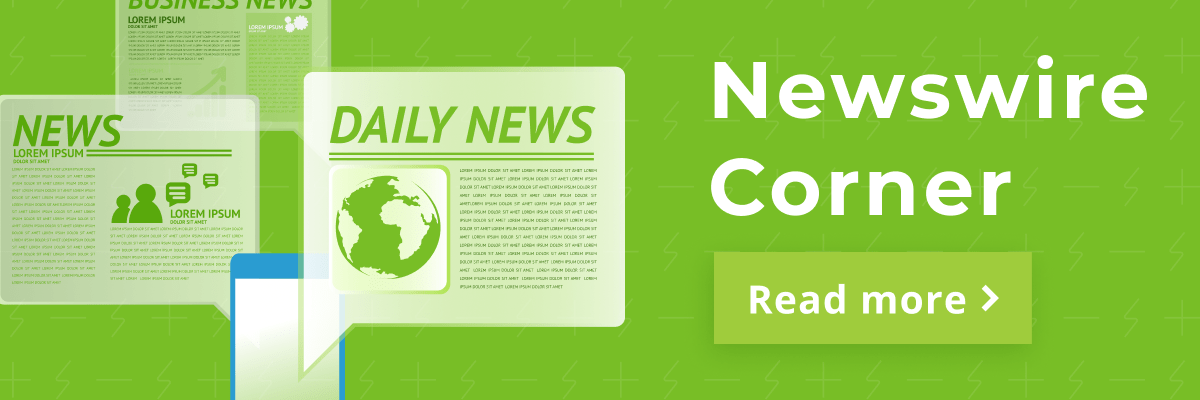
CleanTechnica uses affiliate links. See our policy here.