Vertical Integration: Tesla’s Secret to Overcoming Challenges
Last year proved to be extremely challenging for the auto sector. Supply chain issues, a global chip shortage, and a pernicious pandemic plagued the industry. However, an unorthodox strategy at Tesla proved invaluable when facing tough times in 2021 — vertical integration.
Tesla attended the 4th China International Import Expo, "unfolded" Shanghai Gigafactory to Expo. pic.twitter.com/AWlrRuqhXX
— Tesla Asia (@Tesla_Asia) November 8, 2021
Tesla showcases its electric cars in various stages of production at the China International Import Expo (Twitter: Tesla Greater China)
Jack Ewing reports in the New York Times, “Just a few years ago, analysts saw Mr. Musk’s insistence on having Tesla do more things on its own as one of the main reasons the company was struggling to increase production. Now, his strategy appears to have been vindicated.”
“In recent decades, the conventional auto wisdom had it that manufacturers should concentrate on design and final assembly and farm out the rest to suppliers. That strategy helped reduce how much money big players tied up in factories, but left them vulnerable to supply chain turmoil,” writes Ewing.
In contrast, Tesla tightly controls the tech inside the car. “Tesla has fewer boxes,” said Phil Amsrud, a senior principal analyst who specializes in automotive semiconductors at IHS Markit, a research firm. “The fewer the components you need right now, the better.”
“It’s a more streamlined approach.” says Mr. Amsrud. And, unlike traditional automakers mired in antiquated gas-engine technologies, “Tesla started from a clean sheet of paper.”
Wedbush analyst, Dan Ives, talks about Tesla overcoming challenges in 2021 and forecasts what’s ahead in 2022 (YouTube: CNBC Television)
In addition, Elon Musk’s ongoing emphasis on in-house software development helped him outsmart competitors. “Tesla, born in Silicon Valley, never outsourced their software — they write their own code,” says Morris Cohen, a professor emeritus at the Wharton School of the University of Pennsylvania who specializes in manufacturing and logistics.
“Tesla controlled its destiny,” explains Professor Cohen.
“Doing more on its own also helps explain why Tesla avoided shortages of batteries, which have limited companies like Ford and G.M. from selling lots of electric cars. In 2014, when most carmakers were still debating whether electric vehicles would ever amount to anything, Tesla broke ground on what it called a gigafactory outside Reno, Nev., to produce batteries with its partner, Panasonic. Now, that factory helps ensure a reliable supply,” according to NYT.
“It was a big risk,” said Ryan Melsert, a former Tesla executive who was involved in construction of the Nevada plant. “But because they have made decisions early on to bring things in house, they have much more control over their own fate.”
In turn, according to Bloomberg, “Investors have embraced Tesla Inc. and its meteoric rise.” Why? If there’s an industry-wide EV race, Morgan Stanley’s Adam Jonas says Tesla leads the way. “Think of the EV race as a marathon. Tesla is in the lead at mile number 21. Everybody else is at mile 2 or still tying their shoes.”
Originally published on EVANNEX.
Have a tip for CleanTechnica? Want to advertise? Want to suggest a guest for our CleanTech Talk podcast? Contact us here.
Latest CleanTechnica.TV Video
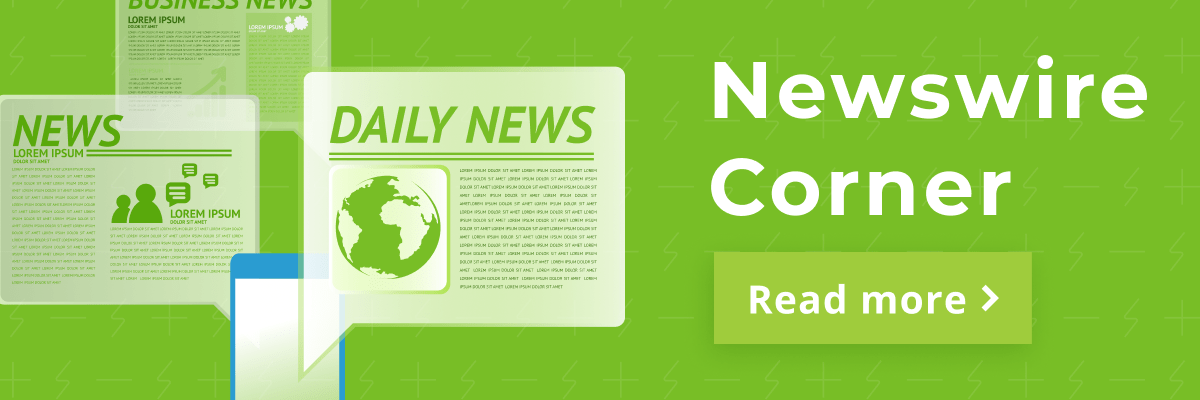
CleanTechnica uses affiliate links. See our policy here.