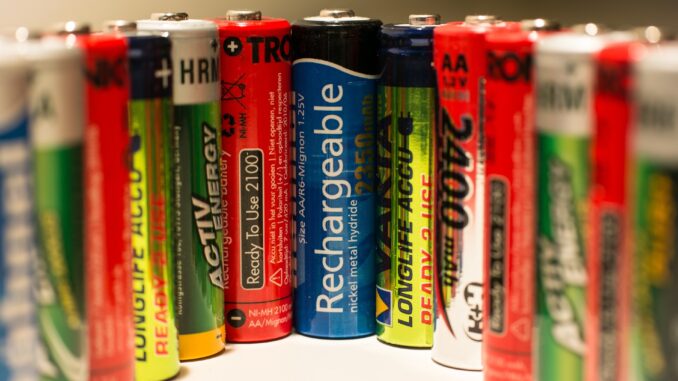
Now that Electric Vehicles have been streamlined, companies are in the process of making them even better and better.
One of the key elements which can improve the performance of an EV is improving its battery pack. If We could improve the battery pack of an ev we can improve the EV altogether and the improvements can be noticed in the,
- Safety of the EV
- The range offered by the EV
- Improved handling (The lighter the battery the lighter the EV)
- Maintenance cost gets reduced
And the list goes on…
So what are the ways we could improve an EV Battery?
But Before answering that, let us look at a few of the factors which has to be considered while designing the battery pack for an EV.
- Batteries cannot operate at full capacity in cold weather. The ideal operating temperature for batteries is between 68°F and 77°F (20°C and 25°C). It’s crucial to keep things at the proper working temperature.
- Over time, natural wear causes batteries to lose some of their storage capacity. The driving experience must not be impacted by this power loss.
- For best performance, battery cells must be balanced, which calls for a constant voltage across the board. During charges, battery cells are rebalanced, but as they get older, they become less capable of doing so. Additionally, the popularity of quick charges is posing a threat to the performance of balancing.
To better understand the complexity behind battery technology and designing, let’s go over the following subjects:
1. What is a Battery Pack
2. The Components of a Battery Pack
What is A Battery Pack?
To power an electrical system, such as an energy storage system (ESS) or an electric vehicle (EV), a battery pack is a device that stores electrical energy. The battery pack has cells that are all interconnected and used to store energy.
Battery packs need a minimum voltage level that a single cell cannot reach to provide adequate power. As a result, several cells are linked together in series to increase voltage.
Small-capacity cells are used in some designs. Cells are linked in parallel to increase capacity and produce the needed battery energy. Parallel cell connections provide power as if they were one huge cell.
Battery modules (or sub-packs) are the many, smaller pieces that make up battery packs. These modules have fewer cells that are linked in series and parallel. They are typically handled safely because they are at a lower voltage.
When only a few cells need to be replaced and they can be done so without having to replace the complete battery pack. EV batteries are typically constructed from four to forty modules connected in series.
Components Of An EV Battery
The most expensive component of an electric car is the battery pack. It is a complicated system with many different parts. Here are a few of the key elements.
Cells
The most crucial parts of a battery pack are the cells. The chemistry of the cell refers to the materials that make it up. Different battery chemistries can provide batteries with varying performances and specifications.
Power cells and energy cells are the two main categories of cells.
Depending on the application, other variations can offer the ideal trade-off. The lithium-ion cell (li-ion cell) is the most popular chemical in the EV sector. Alternative combinations, such as Nickel-Metal Hydride (NiMH), which has a little better lifetime, are occasionally used.
Connectors
Cells and collections of cells are connected in series or parallel via electrical connectors like busbars, wires, or other distribution conductors.
Typically, laser welding or ultrasonic bonding is used to make these connections. Fasteners can be used to mechanically connect busbars between modules.
Thermal interface Materials
To mechanically attach battery components while enhancing the thermal characteristics between surfaces, thermal interface materials (TIMs) such as pastes, adhesives, and gap fillers are injected between them. TIMs are turning into crucial components with the development of the structural battery pack.
Battery Management System
Cells are safeguarded by the Battery Management System (BMS), which keeps an eye on vital indicators like voltages, currents, and temperatures.
It interacts with several systems, including temperature control and powertrain management, and is in charge of cell balancing (to keep the cells operating at their best at the appropriate voltage). It also has safety features that, if necessary, may turn the battery off.
Battery Thermal Management System
The battery’s thermal needs are met and the battery’s cells are protected by the Battery Thermal Management System (BTMS), which regulates the heat in the EV’s interior and drivetrain.
A heat exchanger, tubes, hoses, cold plates, pumps, valves, and temperature sensors are just a few of the parts that make up the BTMS.
Contactor system
The battery management system is in charge of the switch known as the contactor system. It can interrupt the flow of current to the traction motor and other high-voltage components from the main battery to the high-voltage bus.
Housing
The Housing is a strong shell that shields the battery from elements including salt, dust, and water. It aids in preserving the battery’s precise temperature and electrical insulation and guards against rust and sluggish shorts.
The Communications System makes sure that the electric vehicle’s various parts can communicate with one another. The CAN bus protocol is the most popular.
So you see the Battery Pack used in an EV is not as equal to your normal cell phone battery.
Now let us look into the most popular EV battery chemistry which is the Li-Ion Battery
The Draw Back With LI-Ion Battery
Although conventional lithium-ion batteries are getting better, they still have some drawbacks, partly due to the way they are built. Two electrodes, one positive and one negative are sandwiched around an organic (carbon-containing) liquid to make up a lithium-ion battery.
Electrically charged lithium ions (or particles) move from one electrode to the next through the liquid electrolyte as the battery is charged and discharged.
The liquid electrolyte in that design has the potential to catch fire and become volatile at certain voltages and temperatures. It doesn’t mean that EV batteries are risky they are generally safe under normal usage, but the risk is still there.
The inadequacy of lithium-ion batteries for usage in automobiles is another issue. The problem is, large, bulky battery packs take up room and add to the overall weight of a vehicle, which lowers its fuel efficiency.
But it is challenging to reduce the size and weight of lithium-ion batteries while retaining their energy density, or the amount of energy they can hold per gramme of weight.
The Solid State Batteries
Researchers are working to create an all-solid, or “solid-state,” version of the lithium-ion battery to address these issues. They swap out the central liquid electrolyte for a thin, solid electrolyte that can withstand a wide variety of temperatures and voltages.
They use a high-capacity positive electrode and a high-capacity lithium metal negative electrode with that solid electrolyte; these electrodes are both much thinner than the typical layer of porous carbon.
These modifications enable a significant reduction in the battery’s overall size while maintaining its energy-storage capacity, leading to an increase in energy density.
The two benefits of a solid-state battery that are generally mentioned the most are,
1. improved safety
2. Greater energy density.
3. Smaller in size compared to LI-Ion Batteries without reducing the range
It is to be noted that these are all hoped for theoretically and have to be tested and verified.
Thinking beyond The Lab
The researchers in the field suggest three broad questions that can help identify potential constraints on future scale-up as a result of materials selection. These questions are based on industry experience with current lithium-ion batteries.
First, when production goes up, may issues with materials availability, supply networks, or price volatility arise with this battery design? (Note that this study does not address the environmental or other issues created by expanding mining operations.)
Second, will making batteries from these materials require challenging manufacturing processes where parts are likely to malfunction?
Third, do the manufacturing precautions required to guarantee a high-performance product based on these materials ultimately result in reduced or higher battery production costs?
All these questions and answers to those questions are very important and vital. That is, if only we have satisfying answers to the questions, we will be able to move forward with the mass production of solid-state batteries.
Resources & Accessibility
There are two basic types of materials in the universe of solid inorganic electrolytes: oxides, which contain oxygen, and sulphides, which include sulphur. The researchers concentrated on one electrolyte that showed promise in each class and looked at the main issues with each of them.
The researchers gave the sulphide known as LGPS a mixture of lithium, germanium, phosphorus, and sulphur. They concentrated on germanium due to availability concerns because germanium is typically not mined on its own. It is a byproduct of the mining of coal and zinc.
The amount of germanium generated annually over the last six decades as a result of coal and zinc mining was compared to the amount that could have been created by the researchers to determine its availability.
The results revealed that even recently, 100 times more germanium could have been produced. Given that supply potential, scaling out a solid-state battery based on an LGPS electrolyte is not anticipated to be restricted by the availability of germanium.
Components and Processing
The difficulties of the manufacturing process and how it may affect pricing are additional factors to take into account when evaluating a battery design’s capability for scaling up.
A solid-state battery must always be manufactured in many steps, and any step failure increases the price of each cell that is successfully manufactured.
The researchers investigated the effect of failure rate on the overall cost for chosen solid-state battery designs in their database as a proxy for manufacturing complexity. They concentrated on the oxide LLZO in one instance.
A big sheet of LLZO that is thin enough to be used in a high-performance solid-state battery but likely to deform or shatter due to the material’s exceptional brittleness at the high temperatures necessary in manufacturing operations.
They also created a model of four crucial processing processes involved in the assembly of LLZO-based batteries to assess the financial effect of such failures. Each step’s cost was determined using an assumed yield, or the percentage of all units that were handled without error.
The yield with the LLZO was substantially lower than with the other designs they looked at, and as the yield decreased, the price per kWh of battery energy increased noticeably.
For instance, cost increased by around $30/kWh when 5% more units failed during the final cathode heating stage, which is a significant rise given that the industry standard goal cost for such batteries is $100/kWh.
Materials and Performance
The “interfaces” or points where one component meets another present one of the key design issues for all-solid batteries. Materials at those interfaces may become unstable during production or use. According to the experts, atoms might start moving in directions they shouldn’t, and battery performance may suffer.
As a result, a lot of study is put into developing strategies for stabilising interfaces in various battery designs. Many of the suggested techniques improve performance, which lowers the cost of the battery in terms of dollars per kWh.
However, putting such solutions into practice typically requires more time and resources, which raises the price per kWh in large-scale manufacturing.
Conclusion
In the scientific world, we can come up with a lot of magic beans which can perform miraculous things. But to get any benefits from those advanced technologies, we should be able to do the process repeatedly on a large scale which is called mass production.
That is true in the case of solid-state batteries as well. On one hand, solid-state batteries solve a lot of issues and demerits possessed by the conventional LI-Ion battery pack but on the other hand, mass-producing solid-state batteries is a bit problematic.
Let’s hope that researchers and manufacturing engineers be able to produce safe, reliable EV battery packs cheaply.