In its quest to innovate for zero-emission mobility, Henkel partners with OEMs and battery manufacturers to solve the biggest challenges around EV battery technology.
E-mobility design goals that advance EV performance, reliability, and safety, set an ambitious standard for battery R&D engineers. Navigating regulatory compliance, championing carbon emission reductions across the entire value chain, and accelerating development timelines all add complexity to the design process of battery electric vehicles. Successfully addressing these challenges relies on innovation as a key factor.
Complex design requirements call for innovative solutions
EV customers want a longer driving range, faster charging, and affordable costs. Moreover, crash performance and thermal safety are vital priorities for OEMs and battery manufacturers. OEMs and their battery development partners are stepping up to facilitate the transition to e-mobility successfully. On the journey to making e-mobility happen, Henkel enables original equipment manufacturers (OEMs) and battery manufacturers to solve their design and assembly challenges with innovative material solutions.
Henkel’s e-mobility and innovation capabilities continue to expand across a number of targeted initiatives. For example, over the past few years, Henkel has launched:
- An experienced and diverse ‘Fuel the Future’ battery innovation team;
- A new state-of-the-art Battery Engineering Centre;
- Advanced modelling and simulation capabilities through digital twin integration;
- New patents and market-first multi-functional product formulations; and
- A dedicated team of experts for debonding technologies.
In this article, we’ll attempt to cover some of these examples in greater detail, showcasing the innovation synergies offered by Henkel’s highly capable organisation.
‘Fuel the Future’ team
To anticipate and address challenges and solutions in battery technology and materials, Henkel has brought together a global team of battery experts named ‘Fuel the Future’. The team comprises industry experts in key topic areas such as battery safety, debonding and battery recycling, cell manufacturing, and more.
They work directly with customers and deepen Henkel’s connections in the battery ecosystem. In addition to direct customer contact, these industry insiders participate in associations and represent Henkel at conferences as thought leaders.
New battery engineering centres to advance e-mobility
Henkel expanded its investment in e-mobility by opening a brand-new facility that takes customer collaboration to the next level. To help customers fast-track solution development for pivotal innovation areas such as battery safety, sustainability, and thermal management, Henkel now operates a Battery Engineering Centre within its €130m ‘Inspiration Centre Düsseldorf.’ In this first-of-its-kind facility, innovation and product development experts, along with application engineers, collaborate with customers on solving their most pressing challenges, driven by the slogan, ‘innovating for zero-emission mobility.’
At the Battery Engineering Centre, customers will find two distinct facilities: A Battery Application Centre, equipped with production-scale automated dispensing equipment, and a Battery Test Centre, equipped to handle fully charged batteries and test them under various environmental conditions, such as temperature and humidity. As a whole, the Battery Engineering Centre is equipped to handle simulation, dispensing, testing, and analysis projects on all types of battery systems.
Advanced modelling and simulation
Leveraging vast knowledge of materials and decades of data collection, Henkel’s advanced modelling and simulation capabilities help virtually predict performance of materials under a variety of different conditions. Henkel’s modelling and simulation experts create ‘digital twins’ of customers’ batteries and virtually apply different combinations of materials to them. This helps save time and resources, as well as identify the most favourable combination of materials.
When it comes to the battery development process, in particular, customers work with Henkel to model and simulate targeted safety and efficiency through thermal management and thermal runaway management, employing numerical finite element methodologies (FEMs) and system simulations to provide quick verifiable results.
Examples of virtual models used to simulate real-world battery scenarios include fast charging, acceleration, dynamic load, and thermal runaway load. Additionally, simulations help predict thermal performance metrics such as temperature distribution, heat transfer efficiency, and effective cooling power required for the battery pack. High-quality simulations like these can predict how optimised Henkel materials will help the battery system mitigate heat in a potential thermal event.
Leveraging big data in material formulations
Conventional formulating is extremely complex, and Henkel has put in many decades of work creating, understanding, and documenting the vast array of formulas in its e-mobility product portfolio. This big data resource houses the thousands of discoveries and knowledge amassed to date. It indeed empowers Henkel to simulate material behaviour under a variety of circumstances with different physics and performance parameters. This eliminates repetitive tasks by allowing big data to inform digital material models, subsequently growing the depth of available data to continuously speed innovation for Henkel customers.
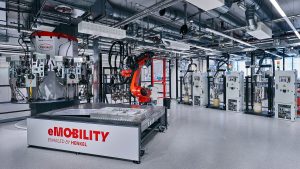
New innovations reinforcing a comprehensive product portfolio
New, bespoke formulations that drive the best solutions for safer, more efficient, and more sustainable batteries are outcomes of Henkel’s innovation endeavours that seek to expand functional integration across key Henkel adhesive technologies.
For instance, Henkel has developed serviceable gasketing material in the form of a patented, removable seal that makes accessing the battery box faster and easier. This simplifies battery pack lid removal for servicing and reuse, repurposing, or recycling without damaging the battery box structure.
Inside the battery cells, Henkel offers conductive electrode coatings that enable the new ‘dry electrode’ manufacturing process, allowing battery manufacturers to produce battery cells in a more sustainable, productive, and efficient way.
Additionally, Henkel offers a variety of battery safety materials, such as battery safety coatings, which can be efficiently produced and easily applied, offering greater confidence to battery manufacturers that their systems will respond reliably and effectively in the rare event of a thermal runaway.
Looking ahead: The future of zero-emission mobility
By combining superior products with modelling and simulation capabilities and real-world testing and validation, Henkel puts OEMs and battery manufacturers on track toward proven solutions that support safe, sustainable, efficient, and affordable battery systems.
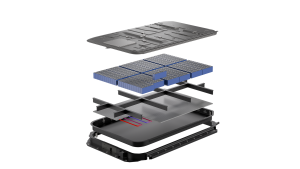
Henkel has stepped up with bold investments in R&D and innovation, rethinking battery design and assembly, and challenging assumptions. Through the opening of the Battery Engineering Centre, Henkel is setting the example now and into the future with an unparalleled combination of modelling, simulation, product innovation, performance testing, and real-world validation.
The upcoming launches of the Battery Engineering Centres in the US and China are set to accelerate e-mobility solutions on a global scale further and faster than ever before.
For more information on e-mobility or other services along the automotive value chain, visit Henkel Adhesive Technologies at: www.henkel-adhesives.com/emobility
Please note, this article will also appear in the seventeenth edition of our quarterly publication.