Honda Joins Race for High Tech 3D-Printed Metal Car Parts
The auto industry’s thirst for 3D-printed car parts is heating up, and the latest development is a doozy. The US startup Seurat Technologies has just closed a $99 million Series C funding round for its new 3D-printed metal technology with new investor Honda on board. Returning for the Series C round are other automakers and suppliers, including Porsche, Denso, and the Ventures arm of General Motors.
$99 Million For 3D-Printed Metal Car Parts
The $99 million in Series C funding for Seurat is a good indication that the auto industry is bullish on 3D-printed car parts. Also referred to as additive manufacturing, 3D printing offers the potential to save energy, reduce waste, trim manufacturing timelines, increase throughput, and pump more flexibility into design and materials (check out our 3D printing archive here).
Depending on the industry, 3D printing systems also open up the potential to cut costs and reduce environmental impacts by downsizing factories, localizing production, and reducing the need for warehouse storage space.
Seurat Technologies launched its investor journey back in 2016, when it raised $3.41 million in a seed funding round. Series A funding followed in 2018, with GM Ventures and Porsche among those chipping in for a total of $13.5 million. The next big step was a $41 million Series B round, closed in 2021.
The GM connection hit the CleanTechnica radar last year, when we noted that the automaker had put up stakes in a group of clean tech startups including Seurat.
Seurat has been rather busy since then. For the record, the Series C round was spearheaded by the NV Ventures branch of NVIDIA along with the climate-focused Technology Impact Fund under the Capricorn umbrella.
The list of series C investors also includes Cubit Capital, Ventures, SIP Global Partners, Maniv Mobility, and Xerox Ventures.
3D Printed Car Parts: The Pixelation Difference
If the name Seurat sounds like a reference to the 19th century French painter Georges Seurat, it is. The post-impressionist artist was famous for popularizing a sophisticated pixelation system in the world of fine art. The technique is echoed by the Seurat Technologies 3D printing system, as elaborately explained by the company’s co-founder James DeMuth in a company blog entry posted in February of 2021.
The new system arose from the challenge of fabricating the reaction chamber for a laser-driven fusion system at the US Department of Energy’s National Ignition Facility in California, where DeMuth worked before launching Seurat.
The reactor material had to be a metal that could withstand wide variations of temperature — including a peak of nearly 1,100 degrees Fahrenheit — without cracking.
DeMuth and his team concluded that deploying additive manufacturing on a steel nanoparticle composite was the way to go. However, existing 3D printing methods sacrifice speed for precision and vice versa. The choice, as calculated by DeMuth, was to wait almost 200 years for their 3D-printed steel nano-composite to come out of the printer, or settle for an inferior product.
Since neither choice was acceptable, the team chose neither.
“We needed to come up with a way to scale while maintaining resolution. We needed to break the coupling between resolution and print rate,” DeMuth explained. “What better way to accomplish this than to pattern the laser? What if every pixel could function as an individual laser?”
Group Hug For US Taxpayers
DeMuth and his team found the key to a solution at NIF, which is run by the Energy Department’s Lawrence Livermore National Laboratory.
The Livermore lab had previously developed a pixelated laser system called OALV, or Optically Addressed Light Valve. The system separates one laser beam into many individual parts, rather than trying to combine different laser sources in one operation.
OALV was initially developed to support the lab’s LEOPARD (Laser Energy Optimization by Precision Adjustments to the Radiant Distribution) system, which won an R&D 100 award in 2012. By 2017, the lab was promoting it as a new, improved tool for fabricating 3D-printed metal products, enabling additive manufacturing to produce larger parts at faster speeds with greater precision than possible with existing devices.
Seurat completed the public-private collaboration in January 2016, when it secured the technology license from the Livermore lab for its new patented, 2.3 million pixel Area Printing technology.
The 3D-Printed Car Of The Future: Whatever Happened To Local Motors?
On its part, Honda is looking forward to the fruits of its investment in Seurat. “Seurat has an innovative concept and technologies for metal additive manufacturing, and Honda has high expectations for their future potential,” explained Manabu Ozawa, Honda’s Managing Executive Officer, in a press statement on Monday.
Seurat already has a number of orders for 3D-printed parts in its pipeline. Next steps include manufacturing the Area Printing system for deployment at or near the point of use, where the customer is located.
If this is beginning to ring some bells, you may be thinking of the US startup Local Motors, which received support from the Energy Department’s Oak Ridge National Laboratory in Tennessee to realize the vision of a 3D-printed electric car that could be fabricated and assembled in local microfactories.
Local Motors never got all the way there, but a 3D-printed aircraft is in the cards. When the company folded its intellectual property was acquired by the aviation startup RapidFlight, for use in unmanned aircraft.
“With this acquisition, RapidFlight gains access to Local Motors’ extensive intellectual property resources, including patents, designs, and engineering expertise,” RapidFlight explained.
RapidFlight anticipates that the treasure trove of knowledge will enable it to introduce new products in a matter of weeks rather than years, so stay tuned for more on that.
Follow me @tinamcasey on Bluesky, Threads, Post, LinkedIn, and Spoutible.
Photo (cropped): An elaborate 3D-printed metal form created with new Area Printing additive manufacturing technology (courtesy of Seurat Technologies).
Have a tip for CleanTechnica? Want to advertise? Want to suggest a guest for our CleanTech Talk podcast? Contact us here.
Latest CleanTechnica.TV Video
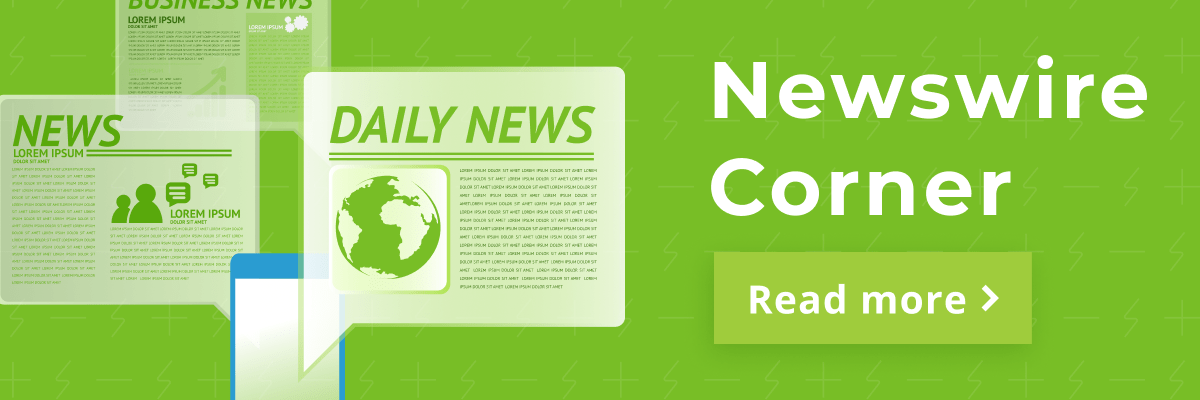
CleanTechnica uses affiliate links. See our policy here.