The electric vehicle revolution is well underway, promising a greener, more sustainable future for the automotive industry. However, despite the growing popularity of electric vehicles (EVs), several significant hurdles are obstructing their widespread adoption. At the forefront of these challenges are supply chain issues, particularly concerning critical components like batteries. Among the most pressing concerns is the heavy reliance on rare and essential minerals, including lithium, cobalt, and nickel, which are indispensable for battery cathodes. We’ve written before about the human rights and environmental issues with mineral mining, and that’s something we’re continuing to learn about. This blog post is more focused on the economic side. Though the supply chain for these vital materials is far from stable, and the necessary infrastructure is not yet fully developed, the last year has seen some significant progress – particularly thanks to the Inflation Reduction Act.
Supply Chain Problems & “Green Metals”
Supply chain dynamics encompass the fluctuations within supply chains that impact timeliness and the delivery of essential raw materials to manufacturers. The majority of the supply chain issues in the EV market stem from the growing need for “green metals” used in lithium-ion battery production: copper, nickel, and manganese. These materials are not actually that rare or hard to find, but they are usually present in only small amounts, so the problem lies not in finding them, but in extracting and processing them. As governments around the world start investing in electric vehicles and charging infrastructure, the demand for these metals continues to grow and thus cause both higher prices and longer wait times as supply chains adjust to this new demand.
This issue is further exacerbated by countries increasing their control of access to essential commodities, such as these green metals. For example, Indonesia completely banned the exports of nickel ore in 2020 and limited trade to only refined nickel products. This policy forced companies to invest money and build nickel refineries in Indonesia instead of shipping raw nickel abroad. This greatly helped the economy of Indonesia and made the country a lot of money (increasing revenue from $3 billion to $30 billion in two years), but it also increased the price of nickel and limited access to raw materials. The Philippines and Zimbabwe have plans to enact similar regulations with their nickel and lithium ores. While these policies bolster local economies, they also inflate commodity prices and restrict access to crucial raw materials. These countries have a vested interest in protecting their natural resources from foreign powers and developing their local economies. China’s role in the mining and processing of these minerals has further complicated the battery supply chain. China currently owns roughly 67% of lithium refining projects around the world, and this stronghold over these minerals is not expected to diminish in the coming years.
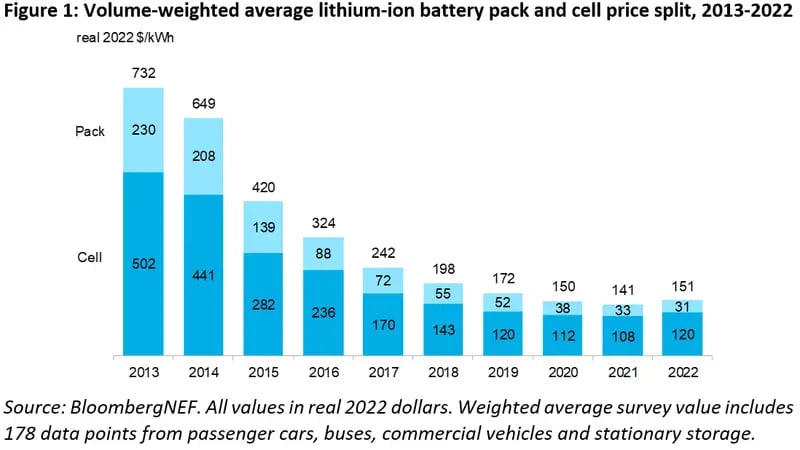
These decisions have heightened anxiety within the manufacturing sector, where there is now apprehension that these increased regulations could potentially lead to further resource protectionism, which will drive up the prices of critical commodities and hinder access to raw materials. Ultimately, the high extraction costs of green metals decrease the likelihood of adequately meeting demand for the EV market, slowing down production and increasing the final cost of electric vehicles.
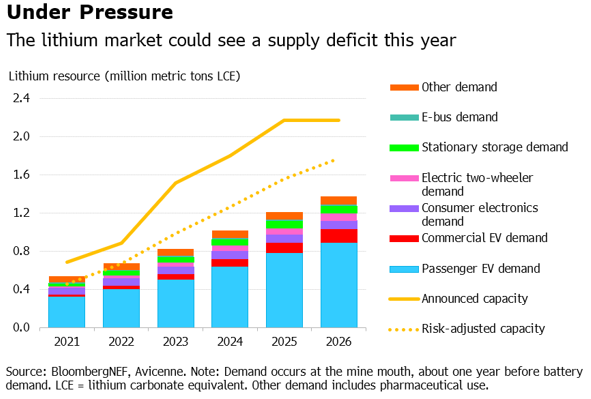
Some Good News
Several potential solutions exist, such as technological advancements in battery technology and finding alternative materials for batteries, battery recycling, and encouraging local mining with strong social and environmental protections.
Technological Advancements
Further development is already underway to find alternatives to nickel, manganese, and cobalt (NMC) in battery cathodes, with one such alternative, lithium iron phosphate cathodes (LFP), gaining popularity. LFP is cheaper and can help boost performance. Tesla is already using LFP batteries in some of their models, and manufacturers like Ford and Volkswagen also announced that they plan to utilize this chemistry in some of their electric vehicles too. Research into solid-state batteries has been pumping up in recent years, as well, and several automakers, including Mercedes-Benz and Toyota, have invested heavily in this technology. This technology replaces the liquid electrolyte in lithium-ion batteries with solid ceramics, which allows for more energy storage in the same physical space and faster charging times. Sodium-ion batteries are another developing technology that completely replaces lithium with sodium, a cheaper and more widely available material than lithium.
Battery Recycling
Another necessary step in reducing the demand on the supply chain is establishing strong recycling practices with a circular economy of batteries that encompasses their entire lifespan. Analysts from the National Renewable Energy Laboratory have found that recycling and reusing lithium-ion batteries has the potential to stabilize the supply chain, reduce resource mining and extraction, and lessen environmental degradation. By improving infrastructure to better handle the recycling of current and future batteries, the US can create a circular economy in which value and minerals are extracted from older batteries for multiple lifespans. Currently, Tesla is able to recycle 92% of old battery cell metals and materials at a rate of 50 tons of recycled material per week.
A former Tesla chief technology officer, JB Straubel, founded a startup, Redwood Materials, that recycles batteries and other e-waste. Recently, Redwood Materials raised $1 billion in private equity and was given a $2 billion loan commitment from the U.S. Department of Energy to expand its recycling operations in Nevada. The company’s model focuses on recycling used EV batteries, dismantling them to extract valuable metals such as nickel, copper, cobalt, and lithium, and then repurposing them to manufacture fresh components for new EVs. Their primary objective is to increase domestic production of batteries, a strategic move aimed at mitigating global trade and supply chain issues. Redwood, and other companies with similar missions that are working to maximize the utilization of recycled materials, can help offset the environmental impacts of EVs and lower the carbon footprint of the transportation sector in the United States.
Domestic Mining
Lastly, an increase in local mining can help elevate the pressure on the supply chain. The United States has been slow to extract lithium from the earth, currently only producing roughly 1% of global lithium. In theory, the US, with over 750,000 tons of recoverable lithium, can meet the growing demand of an estimated 75,000 tons of lithium per year by 2025. But mining has lagged behind demand, with battery production capacity growing twice as fast as raw lithium supply. General Motors (GM), the parent company of Chevrolet, Cadillac, and GMC, plans to manage and control its own supply chain by investing $650 million into lithium mining. Through a partnership with Lithium Americas, GM estimates they can mine enough lithium to produce up to 1 million EVs every year. This level of raw extraction and processing will certainly help with any future supply chain issues and can potentially lead to other automakers entering into the mining industry to secure enough materials for the production of their own EVs. This also raises the fear of further environmental degradation, so with this new mining must also come strict environmental regulations.
The Inflation Reduction Act is already having an impact.
The Inflation Reduction Act, signed by President Biden in 2022, has already driven massive investments, both public and private, into domestic mining and processing of raw materials for EV batteries. However, a less publicized clause in the act has helped bolster recycling. This clause “automatically qualifies EV battery materials recycled in the U.S. as American-made for subsidies, regardless of their origin.” So, the vehicles produced by any automaker that uses recycled batteries qualify for current federal tax incentives (as long as they are also assembled in North America and meet the price requirements). This initiative marks the beginning of a manufacturing resurgence in the United States, as the recycling provisions established by the IRA are driving a surge in U.S. factory construction while also motivating automakers to intensify their efforts in battery recycling research. Just recently, the US Department of Energy announced an additional $192 million will be available for companies working to improve battery recycling in the United States.
This is just the beginning.
The electric vehicles market’s future hinges on overcoming these intricate supply chain challenges and securing a sustainable source of critical materials. The high extraction and processing costs associated with green metals cast a shadow on the prospects of meeting the surging demand for EVs, slowing down production and escalating the ultimate cost of electric vehicles. To continue advancing toward a cleaner automotive future, industry players, policymakers, and manufacturers must collaborate on innovative solutions that ensure a stable supply chain while balancing economic and environmental considerations. Only then can we reach full EV adoption around the globe.
Comments