Volkswagen Claims New Dry Battery Process Will Save Hundreds Of Dollars Per Car
We’ve said it many times, many ways. Battery technology is not a static thing. Hundreds of companies and laboratories around the world — including Oak Ridge National Laboratory — are searching high and low for the next battery technology that will lead to less expensive electric cars with longer range and faster charging. On that front, Volkswagen says it has come up with a new dry coating process that will allow it to lower the price of its electric cars by several hundred dollars.
According to Der Spiegel (paywall), Volkswagen intends to bring a new dry coating process for electric car batteries into large-scale production. Dry coating reduces energy consumption in the production of battery cells by 30%, which could lower the cost of electric cars by several hundred euros per vehicle.
Volkswagen Completes Battery Testing Phase
Sebastian Wolf, a board member of the Volkswagen battery subsidiary PowerCo, said recently that the electrode dry coating method has proven viable in internal tests, which has led PowerCo to invest further in the process and install a pilot line in a laboratory near Salzgitter, Germany. PowerCo’s first battery factory will be located in Salzgitter, part of a plan by Volkswagen Group to make its electric vehicle supply chain more vertically integrated, particularly when it comes to manufacturing the batteries that will power its electric cars in the future. VW is also building a large battery factory in Canada.
According to Wolf, Volkswagen has been researching the new dry coating process with partners since 2020, and expects to use it in the production of millions of battery cells by the beginning of 2027. To date, the company has invested approximately €40 million into researching the dry coating technology.
A number of companies and research institutions worldwide are already working on dry-coating processes for electrodes. A conventional lithium-ion battery manufactured today usually consists of a metal foil covered with a thin coating that contains the active components that make energy storage possible.
The coating process is typically carried out with a semi-liquid paste produced from active materials that include conductive blacks and binders together with a solvent. The paste is then spread as a wet layer on the metal foil — usually copper. Enormous production lines with very long drying distances are needed for the solvent to evaporate afterwards. The dry coating process would make all those steps superfluous and that in turn would dramatically shrink the space needed to manufacture batteries and the energy needed in the drying process.
Among the very active players in this field is an alliance of Siemens, LiCAP Technologies and BW Papersystems. About six months ago, the trio formed a strategic partnership to manufacture and market such equipment for the battery cell industry.
Tesla is also working on dry coating for its large 4680 cells. Most recently, it was reported that Tesla can dry coat the anode but is still struggling with dry coating problems on the cathode.
Volkswagen, 24M, & QuantumScape
Volkswagen is thinking ahead when it comes to future production systems. In 2021, the company invested in the US battery startup 24M Technologies, which goes one step further than the dry coating process with a semi-solid process. Volkswagen has been a licensee since 2021. At that time, it said, “In the future, significant cost optimization in battery production will be achieved by reducing the use of materials and eliminating several steps in the conventional production process. To this end, a new Volkswagen subsidiary will further develop and scale the technology on the basis of 24M’s patent rights for automotive applications.”
Volkswagen had also invested in QuantumScape, another US-based company that is promising to bring solid-state batteries to market. Both QuantumScape and 24M Technologies are targeting the end of this decade before their batteries are ready for commercial production. According to Der Spiegel, the new dry coating process also might not see commercial production until later this decade.
One way or another, the batteries that power electric vehicles in 2030 are still in the laboratory today. Volkswagen thinks it sees an opportunity here, but it’s impossible to know what other battery technology breakthroughs may happen along the way. The future is so unpredictable!
ORNL Solid-State Breakthrough
Earlier in this article we made reference to new research from Oak Ridge National Laboratories that pertains to solid-state batteries. In a research paper published recently in the journal ACS Energy Letters, researchers led by ORNL’s Marm Dixit and colleagues found that isostatic pressing can create thin layers of solid, uniform electrolyte, maintaining a high level of contact between the layers for smooth ion movement. The method works with a variety of battery compositions at different temperatures and pressures.

This process uses fluids and gases like water, oil, and argon inside a machine to apply consistent pressure across a battery component, creating a highly uniform material. With the help of an industry partner that produces this pressing equipment, ORNL researchers found that isostatic pressing could make battery production easier and faster while creating better conditions for energy flow.
Among the promising results, isostatic pressing was found to be extremely successful at low temperatures and with soft electrolyte materials, which are easier to process and which have favorable crystal structures for ion movement. Previously, isostatic pressing of batteries had been done mostly at very high temperatures or at room temperature, but not in between.
“All these materials have their unique advantages that researchers would like to exploit,” Dixit said. “That’s why it’s important that you can do isostatic pressing at anywhere from room temperature to several thousand degrees Fahrenheit: It means you can use anything from polymers to oxides, the whole range of materials.”
This versatility is key to a consistent manufacturing process for the broad variety of solid-state battery designs and materials being developed, Dixit said. Isostatic pressing would also be relatively easy to scale up commercially — a finding that has garnered significant attention as companies race to supply solid-state batteries to car manufacturers. Several leading auto companies have announced their intention to sell electric vehicles that run on solid-state batteries within a few years.
Ilias Belharouak, a corporate fellow at ORNL and head of its electrification section, said solid-state battery technology needs to be perfected for large-scale manufacturing. “Make no mistake, all solid-state batteries are on a journey for the long haul,” he said. “But the isostatic pressing technology, if scalable, would provide a way to assemble the battery layers without impractical external pressures.”
Isostatic pressing has been used for decades in fusion bonding and joining materials. Recently, it has been a tool for eliminating voids and anomalies in 3D-printed parts. However, its testing for battery applications has been limited. ORNL researchers indicated isostatic pressing may also allow manufacturing the three battery layers as a single, dense system rather than creating them separately before joining them.
In the ACS Energy Letters paper, Dixit’s team stressed the importance of pursuing a solid-state battery that can be scaled up for manufacturing. “Effectively addressing this challenge would leapfrog present day battery technology into the next decades by enabling energy dense solid state batteries to meet the burgeoning demands of portable electronics, grid storage, electric vehicles, and aviation applications,” they wrote. Dixit said, “It’s the same material. You’re just changing how you make it while improving the battery performance on a number of fronts.”
And so, the EV revolution continues moving steadily forward.
Have a tip for CleanTechnica? Want to advertise? Want to suggest a guest for our CleanTech Talk podcast? Contact us here.
Latest CleanTechnica.TV Videos
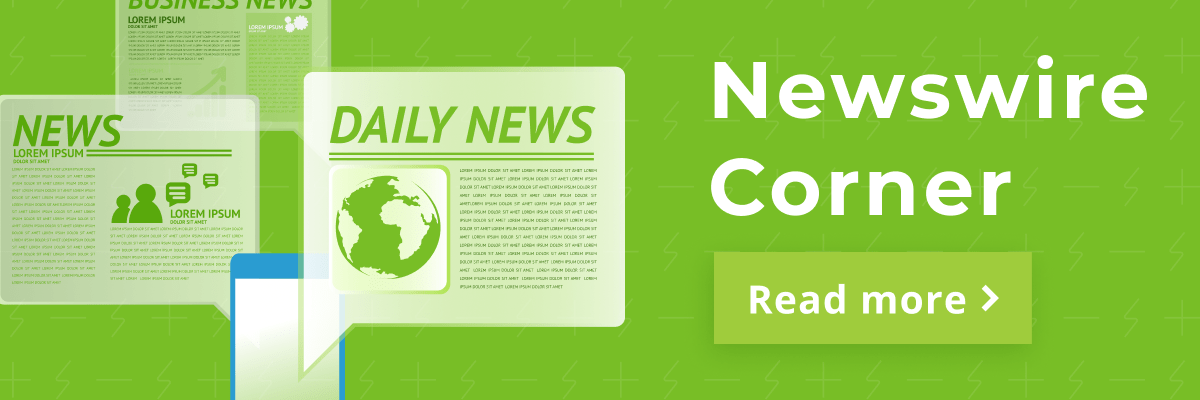
CleanTechnica uses affiliate links. See our policy here.