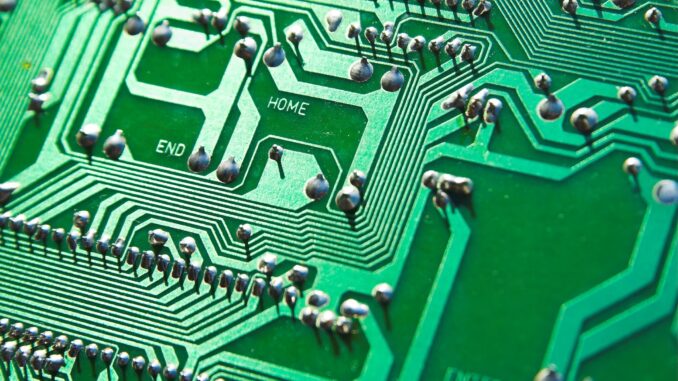
Electric vehicle components communicate with each other through a networked system known as the Controller Area Network (CAN). The CAN bus is a standardized communication protocol that enables various components within an electric vehicle to exchange information and coordinate their functions.
The CAN bus allows for real-time communication between different electronic control units (ECUs) and sensors distributed throughout the vehicle. Each ECU is responsible for controlling specific functions or subsystems, such as the motor controller, battery management system, charging system, braking system, and more.
How do the components communicate using CAN bus?
Here’s how the components communicate using the CAN bus:
- CAN Messages: Information is exchanged between components in the form of CAN messages. Each message contains an identifier (ID) that identifies its purpose and the data it carries. For example, a message might contain vehicle speed, battery voltage, or motor torque information.
- Broadcast and Addressing: In the CAN bus system, messages are broadcasted to all ECUs connected to the network. However, each ECU is designed to filter and interpret only the messages relevant to its functions based on the message IDs. This allows different components to communicate without unnecessary processing overhead.
- Data Transmission: Components transmit data by placing the desired information within the CAN message structure. The information is typically in the form of digital signals that represent specific values or states relevant to the component’s function. Other components can then receive and interpret this data as needed.
- Data Integrity and Error Checking: The CAN protocol incorporates error detection and correction mechanisms to ensure data integrity. It uses checksums and acknowledgment mechanisms to verify the accuracy of the transmitted data and detect errors. If errors are detected, the necessary measures can be taken to handle or correct them.
- Gateway: In more complex electric vehicles, a gateway ECU may be present to manage communication between different CAN networks. It acts as an interface between various subsystems or domains, allowing them to communicate and share information effectively.
CAN in Automotive Industry
The modern automobile may have as many as 70 Electronic Control Unit (ECU) for various subsystems. Traditionally, the biggest processor is the engine control unit. We cannot find Engine control unit in electric vehicle.
There are some other ECUs in a vehicle used for Autonomous Driving, Advanced Driver Assistance System (ADAS), transmission, airbags, antilock braking/ABS, cruise control, electric power steering, audio systems, power windows, doors, mirror adjustment, battery and recharging systems for hybrid/electric cars, etc.
Some of these form independent subsystems, but communication among others is essential. A subsystem may need to control actuators or receive feedback from sensors. The CAN standard was devised to fill this need.
One key advantage is that interconnection between different vehicle systems can allow a wide range of safety, economy and convenience features to be implemented using software alone – functionality which would add cost and complexity if such features were hard wired using traditional automotive electrics. Examples include:
#1 Auto start/stop:
Various sensor inputs from around the vehicle (speed sensors, steering angle, air conditioning on/off, engine temperature) are collated via the CAN bus to determine whether the engine can be shut down when stationary for improved fuel economy and emissions.
#2 Electric park brakes:
The hill hold functionality takes input from the vehicle’s tilt sensor (also used by the burglar alarm) and the road speed sensors (also used by the ABS, engine control and traction control) via the CAN bus to determine if the vehicle is stopped on an incline.
Similarly, inputs from seat belt sensors (part of the airbag controls) are fed from the CAN bus to determine if the seat belts are fastened, so that the parking brake will automatically release upon moving off.
#3 Parking assist systems:
When the driver engages reverse gear, the transmission control unit can send a signal via the CAN bus to activate both the parking sensor system and the door control module for the passenger side door mirror to tilt downward to show the position of the curb. The CAN bus also takes inputs from the rain sensor to trigger the rear windscreen wiper when reversing.
#4 Auto lane assist/collision avoidance systems:
The inputs from the parking sensors are also used by the CAN bus to feed outside proximity data to driver assist systems such as Lane Departure warning, and more recently, these signals travel through the CAN bus to actuate brake by wire in active collision avoidance systems.
#5 Auto brake wiping:
Input is taken from the rain sensor (used primarily for the automatic windscreen wipers) via the CAN bus to the ABS module to initiate an imperceptible application of the brakes while driving to clear moisture from the brake rotors. Some high-performance Audi and BMW models incorporate this feature.
#6 Remote sensors
Sensors can be placed at the most suitable place, and their data used by several ECUs. For example, outdoor temperature sensors (traditionally placed in the front) can be placed in the outside mirrors, avoiding heating by the engine, and data used by the engine, the climate control, and the driver display.
In recent years, the LIN bus (Local Interconnect Network) standard has been introduced to complement CAN for non-critical subsystems such as air-conditioning and infotainment, where data transmission speed and reliability are less critical.
[Ref: Wikipedia Read this post to know more about CAN communication]
Conclusion
Through the CAN bus, electric vehicle components are able to exchange critical data and instructions, enabling the coordination and control necessary for the vehicle’s proper functioning. The CAN protocol provides a reliable and efficient means of communication, ensuring that the various systems in the electric vehicle work together seamlessly.